2020년 여름즈음 뜬금 없이 학교에서 연락이 왔다.
연락의 이유는 공학교육혁신센터에서 주최하는 창의융합인재사관학교 Advanced 과정에
참여할 생각이 없냐는 것이었다. 이 Advanced 과정은 기존에 캡스톤 프로젝트를 진행해봤던 팀을 대상으로
추가 교육과 지원금, 그리고 특허출원의 기회까지 주어지는 과정이었다.
사실 우리는 2019년에 적정기술 사회봉사 캡스톤 디자인 프로젝트에 참여한 적이 있었고,
학교측에서는 많은 팀이 지원하길 바래 우리한태도 참여해보라는 권유차원의 연락이었다.
https://tkwk415.tistory.com/3
[지똥이의 대학일기] 적정기술?
이제 2019년도 지나가고 2020년 1학기 개강을 앞두고 있습니다. (개강이 계속 연기 될 수도 있지만요 ㅜㅜ 코로나) 지난 학기동안 제가 열심히 활동했던 프로젝트인 적정기술 창의설계 프로젝트!!
tkwk415.tistory.com
https://tkwk415.tistory.com/40
[적정기술] 캡스톤 디자인 팀프로젝트, 유압식 카사바 수확기!
2019년, 대학교 2학년 재학 당시 적정기술에 대해 처음 교육을 받게 되었다. 대학 동기 3명이서 여름방학을 맞이하여 함께 시작했고, 그것이 적정기술이라는 분야를 알게 된 때였다. 사실 적정기
tkwk415.tistory.com
위의 나의 글들을 보면 알겠지만 이 프로젝트를 하면서 되게 힘들었고, 다시 도전한다는게 엄두가 나지 않았다.
또한 팀원도 한명 나가게 된 상황이라 두명만 남아있어서 하게되더라도 인원을 추가로 뽑아야 했다.
결론적으로, 우리는 또 해보기로 했다.
대신 우리끼리 정한 참여하는 조건은
1. 인원을 추가로 뽑을것.
2. 기존의 유압식 카사바 수확기보다 발전된 형태여야 할 것.
3. 실제로 제작해볼 것.
이렇게 우리끼리 약속을 하고 우선적으로 팀원을 뽑기로 하였다.
우리는 팀원을 뽑기위해 아이디어를 재설정하고, 어느 분야의 인원이 필요한지 정했다.
우리의 기존의 아이디어는


이런 형태의 아이디어였다. 차량용 가레지 작기처럼 뒤에서 수동으로 유압을 가해주면 앞부분이 위로 상승하게 되는 원리이다. 이에 우리는 기존의 링크시스템에 유압실린더 대신 전기모터를 이용하여 자동식으로 해보기로 했다.
그래서 우리가 필요한 인원들은
1. 간단한 용접과 전기모터 제어에 대한 지식이 있는 인원
2. 전기회로와 간단한 코딩을 할 수 있는 인원
실제로 그래서 자동차공학과의 자작자동차동아리 소속이었던 인원 2명과 전기정보공학과 1명을 추가 영입하여,
우리팀은 5명이 되었다.

그렇게 우리는 꾸준히 자료를 조사하고 회의를 진행했다.
이 과정속에서 이러한 프로젝트의 아이디어가 적절한지에 대해 직접 탄자니아에 거주하시는 카사바농장의 커뮤니티장님과 ‘페이스북’으로 소통하며 본 연구의 필요성을 느낄 수 있었다.


그래서 우리는 믿음을 가지고 프로젝트를 계속해서 진행했다.
그렇게 우리가 제작한 것의 3D 도면은 이러한 형태이다.


작동방식은
1. 보조손잡이를 잡고 당긴다. 이에 와이어가 함께 당겨진다.
(일종의 자전거 브레이크를 연상하면 될 것임.)
2. 와이어가 당겨져 집게의 기계적 메커니즘에 따라 오므려지고 카사바를 잡는다.
(랙과 피니언 기어가 주요 원리)
3. 카사바가 잡힘과 동시에 손잡이에 부착된 압전센서는 입력 값을 아두이노로 전송하고, 이를 통해 모터가 구동된다.
(아두이노를 통한 모터 제어)
4. 내부 장치의 기계적 메커니즘에 따라 집게가 위로 올라가며 카사바를 들어올린다.
5. 카사바가 완전히 뽑히면 보조손잡이에서 손을 떼고 압력신호가 사라짐을 감지하여 모터의 구동이 멈추게 되며,
집게의 랙 부분에 장착된 압축스프링을 통해 원래 상태로 돌아갈 것임.
6. 다음 작물로 이동하여 1~4를 반복한다.
(여기서 구동 시 바닥이 평탄하지 못하고 기계가 구동하며 흔들릴 경우 옆에 있는 지지대를 발을 이용해 바닥에 고정시킬 수 있을 것임.)
제작과정은
<이론 설계 과정>
팀내에서 제작에 경우 크게 3개의 팀으로 나누어져 작업을 하였으며, 기본 모델링은 기계프로그램 팀원들이 맡았으며, 2D Linkage 프로그램을 통해 나온 설계도면을 가지고, onshape와 inventor를 이용하여 3D 모델링을 진행하였다.
이러한 설계를 바탕으로 모터와 배터리의 사양설정과 제품 구매 부분은 자동차프로그램 팀원들이 맡았으며, 원하는 토크 값을 계산하고 이에 맞추어 모터, 체인과 스프라켓을 최적설계 하였다.
또한 모터제어와 배선을 전기정보공학과 팀원이 맡았으며, 모터제어는 아두이노를 이용하였다.
<시제품 제작 과정>
실제 시제품 설계 같은 경우는 자작 자동차 동아리 활동 중인 팀원이 담당해서 진행하였으며, 이 과정에서 최대한 기성품으로 존재하는 부품들에 맞추어 제작을 하려하였으며, 일부부품의 경우는 가공을 맡기기도 하였다. 이 과정에서 많은 시행착오를 겪었으며 원하는 가공이 힘들어 설계를 수정하고 재가공하는 과정을 수차례 반복했다. 부품의 경우 을지로4가의 청계공구상가와 인터넷 주문을 통해 구매하였고, 가공의 경우 을지로4가에 위치한 ‘형제정밀’에서 주로 진행하였다.
시제품 부품을 선정하는 과정에서 고민한 부분은 크게 두 가지이었다.
첫째로 각 부품의 링크가 버텨야 할 힘을 계산하여, 장기간 사용에도 변형을 최소화해야한다.
둘째로 가공비용과 시간을 줄일 수 있는 형태를 고안한다.
이에 해결 방안으로서 3가지 방법을 이용하였다.
1. 볼트 너트 결합을 주로 이용하여 고정력을 높이면서도, 가공오차를 늘리는 방안을 선택해, 가공시간을 줄였다.
이때, 록타이트 본드 등을 이용하여, 너트의 풀림을 방지하였다.
2. 환봉의 끝에 나사산을 절삭해내는 과정을 줄이고, 경량화를 시키기 위해 파이프 끝에 볼트를 용접하는 형식으로
변형하였다.
3. 가공 시간과 비용이 많이 들어가는 집게는 아크릴판 레이저 컷팅을 통해 정밀성은 높이고, 시간과 비용을 줄였다.
그 대신, 큰 T수의 판을 이용해, 충분한 강성을 확보하였다.
이러한 부분 이외에도 같이 부품별 상세 가공방식을 정하고 설계, 가공법고안, 제작, 재설계의 과정을 계속 순환하며, 시제품 제작을 진행하였다.

또한 제작하면서 어려웠던 점은 크게 3개정도 있었다.
첫 번째는 설계시 오차이다. 설계를 하면서 제작시 허용오차를 고려하지 않아서 너무 딱맞거나 너무 헐렁한 경우가 자주 발생했다. 제작과 설계의 약간의 괴리가 있을 수 있음을 전혀 고려하지 못한 설계가 어려운 점이었다.
두 번째는 기계장치들을 사용하면서 충분한 주의사항을 숙지해야한다는 점이다. 그라인더를 이용해 철판을 절삭하는 과정에서 작업환경 근처를 제대로 정리하지 못해서 밧줄이 그라인더 사이에 껴서 크게 다칠 뻔 했던 일을 겪었었다.
세 번째는 배터리 회로작업에서 BMS의 중요성이다. 우리는 리튬이온전지 6개 셀을 직렬연결하여 사용하였고, 팀원중 모터제어 경험이 있던 팀원이 BMS의 중요성에 대해 설명해주었고, 실제로 회로를 짜고 연결하였을때 BMS가 타버렸다...
우리가 회로를 잘 못 구성한 것이었으며, BMS 없이 그대로 만들었다면 아마 폭발의 위험도 있었을 것이다.
+ BMS는 (Battery Manaement System)를 BMS는 베터리의 온도 유지, 배터리 셀 밸런싱 및 안전한 사용을 돕는다.
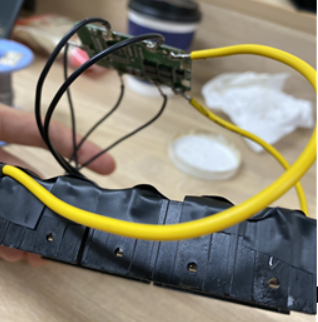

다 제작된 모습은

이러한 형태로 실제로 제작하였다. 실제로 카사바를 수확해보지 못했다는 점에서 아쉬움이 있었지만, 우리가 설계한대로 움직였고 실제로 제작했다는 것에 뿌듯했었다. 또한 대회에서 수상도 하게되어 더욱 뿌듯한 경험이었다.
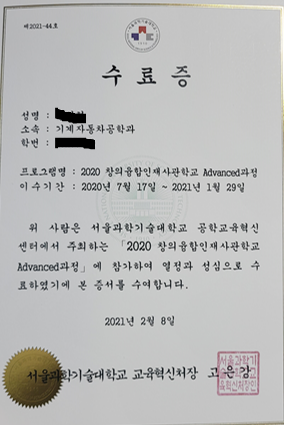

또한 특허 출원의 기회도 주어져서 변리사님과의 4차례정도의 미팅 이후 출원하게 되었다.

'School > 2020' 카테고리의 다른 글
[열시스템 설계] 열교환기 분석 및 최적 설계 프로젝트 결과 (0) | 2022.01.21 |
---|---|
[열시스템 설계] 열교환기 분석 및 최적 설계 프로젝트 준비 (0) | 2022.01.19 |
댓글